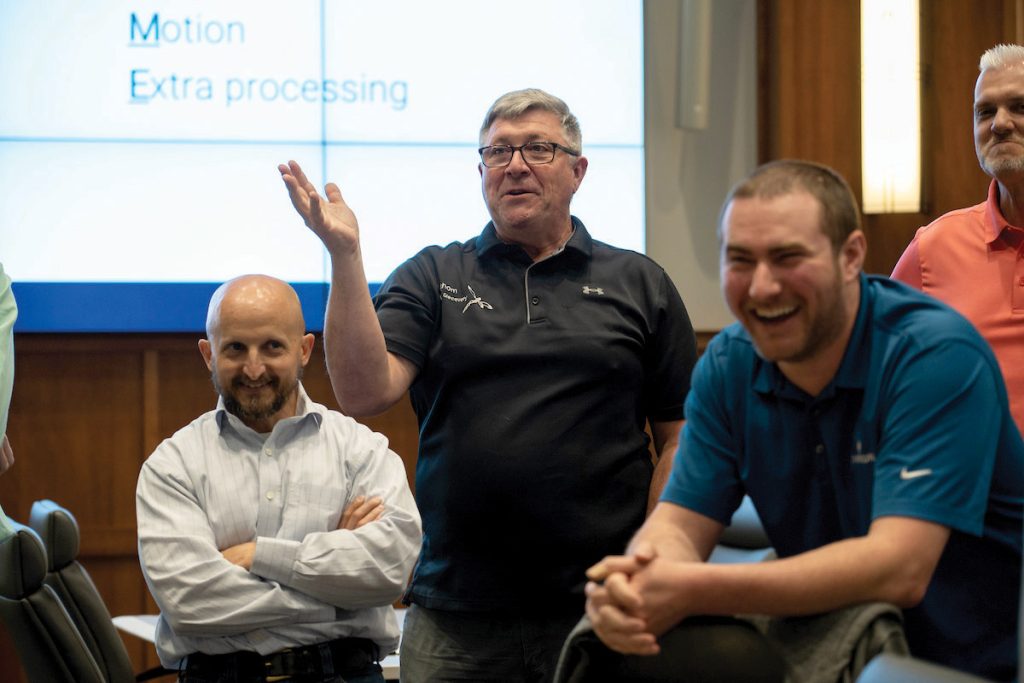
As one of Hoosier Energy’s strategic priorities, continuous improvement has always been a key part of the company’s mindset.
A commissioned team spent over a year developing a program centered around this concept. As a result, Hoosier Energy’s new Rural Electric Continuous Improvement Program (RECIP) is now active.
Starting this past May, all Hoosier Energy employees have been offered the opportunity to learn about the new program through both in-person and remote training sessions. After four months, over 84% of Hoosier Energy employees have undergone training on how they can make their jobs easier and less frustrating while enhancing business operations.
The RECIP training sessions were well received, with over 120 improvement ideas generated — not to mention the discovery of several talented artists. Part of the training program required teams of employees to illustrate some classic “wastes” (tasks that use resources without adding value) discussed by instructors Pat Thomas and Tom Baker of Pathom, a value discovery company that is consulting with Hoosier Energy. The results ranged from stick figures to architectural designs, but overall, the interactive activity helped employees tap into their creativity.
The Continuous Improvement team, led by Continuous Improvement Manager Paul Wayt, will continue to develop these ideas, as well as input new suggestions and work to maximize the opportunities that Hoosier Energy employees are bringing to the table.
Some continuous improvement ideas are already being implemented, including improving visibility at a company exit and reducing the frustrations associated with rescheduling training classes.
“Enhancing Hoosier Energy operations is vital to being competitive in a constantly changing industry,” Wayt said. “This first wave of ideas is identifying opportunities and improvements that affect people every day. These may be small changes, but they are big frustrations. All of these improvements are going to add up in the long run.”
The steps for submitting an idea are simple, as the training sessions showed, and there’s more than one way to do so. In addition to an online form, employees are encouraged to share their thoughts via emails, phone calls or even Post-it® notes.
There’s no wrong way to ensure that continuous improvement continues to happen.